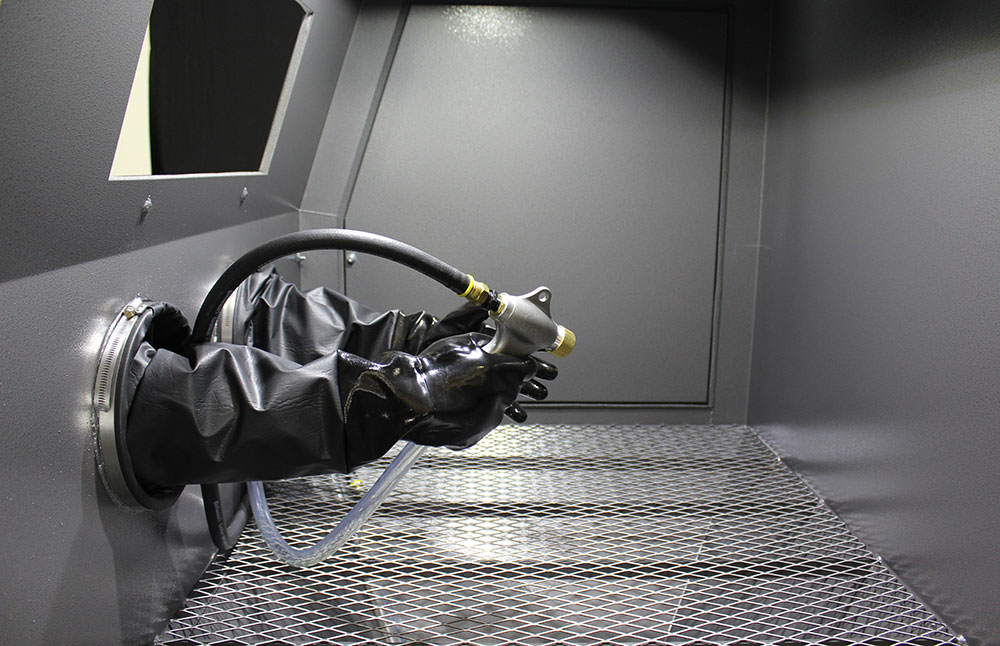
Abrasive blasting is using pressurized air or water to propel abrasive media against a surface to remove coating, corrosion, or contamination.
Also known as sand blasting, grit blasting, or media blasting, abrasive blasting is used to:
- Make a rough surface smooth.
- Make a smooth surface rough.
- Shape a surface.
- Remove surface contaminants or material, like paint, rust, or residue.
- Clean or prepare a surface.
- Finish a surface.
Depending on the type of abrasive media used, the blasted surface with have a smooth, angled, or dimpled profile.
Types of Abrasive Media
Some of the type of abrasive media that may be used in various applications include:
- Steel shot (shot blasting)
- Steel grit
- Glass beads (bead blasting)
- Aluminum oxide
- Crushed glass
- Garnet
- Silicon carbide (carborundum)
- Sodium bicarbonate (soda blasting)
- Plastic grit
- Coal slag
- Pumice
- Copper slag
- Cut wire
- Ceramic grit
- Walnut shells
- Corn Cobs
- Apricot, Peach, or plum stone powder
- Dry Ice
What type of blast media you use is dependent on the effect you want to achieve. Blasting media come in a wide variety of density, hardness, shape, and particle size. It is important to match the right type of abrasive media to both the job at hand, and the method of delivery.
How Abrasive Blasting Works
There are typically three parts to an abrasive blast system:
- Abrasive container, or blasting pot
- Propelling device or mechanism
- Blasting nozzle
In most cases, compressed air or a centrifugally-powered wheel propels the media at the blasted surface. In a blast cabinet, shot blaster, or blast room, the media may be reclaimed and recycled until used up. In outdoor blasting, the used media may be disposed of or recycled.
Dry Blasting and Wet Blasting
The earliest blast cabinets were wet blast cabinets, which used a slurry blasting system: the abrasive media is mixed in water and blasted through a nozzle. This slurry mix would them be re-used.
Dry blasting cabinets were then developed to use a wider range of abrasives. Dry blast cabinets fall into two categories: siphon systems, and direct pressure systems.
In a siphon system bast cabinet, the media is pulled from a hopper in the cabinet, then propelled through the blasting gun using compressed air. A siphon blast system can operate continuously for long periods of time.
With a direct pressure blast cabinet, media is accelerated from a pressure pot, through the blast hose and nozzle. There are a couple of advantages to direct pressure blast systems. One, the blasting process is more efficient, and can be quicker than a standard siphon system. Two, direct pressure systems are capable of handling heavier media than traditional sandblasting cabinets.
One of the main differences between dry blasting and wet blasting is dry blasting uses the impact of the propelled media to affect the blasting surface, wet blasting uses the propulsion of water to clean the surface.
Wet blasting, or dustless blasting, is generally preferred when a more fine-tuned surface profile is desired.
Dry blasting cabinets require a dust collector to pick up and filter the dust from the blasted surface and spent media.
Types of Abrasive Blasting
Abrasive blasting is referred to by several different terms. These terms may refer to the type of blasting media used, the blasting method, the application, or a combination of these.
Here are some of the terms, and what they mean.
Bead blasting uses glass beads, usually at a lower air pressure. Glass bead blasting is usually used in cleaning, deburring, or peening metal surfaces. Blasting with glass beads allows you to remove paint, corrosion, or rust from metal without leaving embedded material. Beads can be used in either dry or wet blasting. Bead blasting leaves a clean, bright finish and a slightly dimpled profile. The smaller the glass beads you use, the smoother the finished surface. Glass beads are non-toxic, with no danger of silicosis (they are not made from silica).
Shot blasting uses spherical steel shot to clean a surface, usually metal. A peening effect is produced by shot blasting, which can add compressive strength to the blasted surface. Shot blasting may take place in a cabinet, if sufficient pressure is used, or in blast rooms or enclosures.
Wheel blasting is used with heavier abrasives, like shot or grit. This method uses a rotating wheel and centrifugal force to propel abrasive media instead of compressed air or water. Wheel blasting was first patented by Wheelabrator in 1932.
Wet blasting was pioneered by Norman Ashworth in the 1950’s. At that time, sandblasting with silica sand was quite popular. But the resulting dust from silica sandblasting caused many people to get silicosis, a particularly nasty respiratory disease. By using water as the abrasive propellant, wet blasting was a way to blast surfaces without creating dust. Wet blasting helps deliver more consistent finishes.
Soda blasting is a mild form of blasting that uses sodium bicarbonate as the abrasive, and compressed air as the propellant. Applications for soda blasting include automotive restoration, rust removal, wood cleaning, graffiti removal, soot remediation, and cleaning of boat hulls. Soda blasting generally uses a much lower PSI than traditional abrasive blasting: about 20 PSI.
Dry-ice blasting uses high-pressure air propulsion and carbon dioxide pellets (dry ice) to clean surface. This process was first patented in 1947, and is today used mostly for cleaning food processing equipment.
Micro-blasting, or pencil blasting is done with specialized bench-top equipment, and is used to blast small surfaces. This is used in glass etching and other highly detailed applications.
A History of Abrasive Blasting
The first abrasive blasting process was patented by Benjamin Chew Tilghman in 1870. The idea likely came from observing nature’s natural pattern of erosion via running water, and wind-blown sand. The earliest abrasive material used was sand, but it was discovered that inhalation of the silica particles led to silicosis, a serious respiratory disease.
By 1893, the invention of the air processor made industrial use of sandblasting possible. In 1904, Thomas Pangborn added compressed air to Tilghman’s original blast apparatus, to create a metal-cleaning sand blasting device. Later, in 1918, the first sandblasting enclosure was built, a precursor to the abrasive blast cabinets of today. This early enclosure had a window for viewing the blasted object, and put a barrier between the workers and the dust particles, so they would not inhale them as easily. This was when exhaust fans were first introduced as well.
The year 1939 saw the introduction of different abrasive media types, many of which are still used today.
Industries That Use Abrasive Blasting
- Shipbuilding and hull cleaning
- Automotive repair and restoration
- Construction and contracting
- Metal finishing
- Welding
- Metal casting and foundry work
- Surface coating or powder coating
- Painting
- Surface preparation
- Glass work, such as etching, decorating and engraving
- Concrete
- Monument engraving